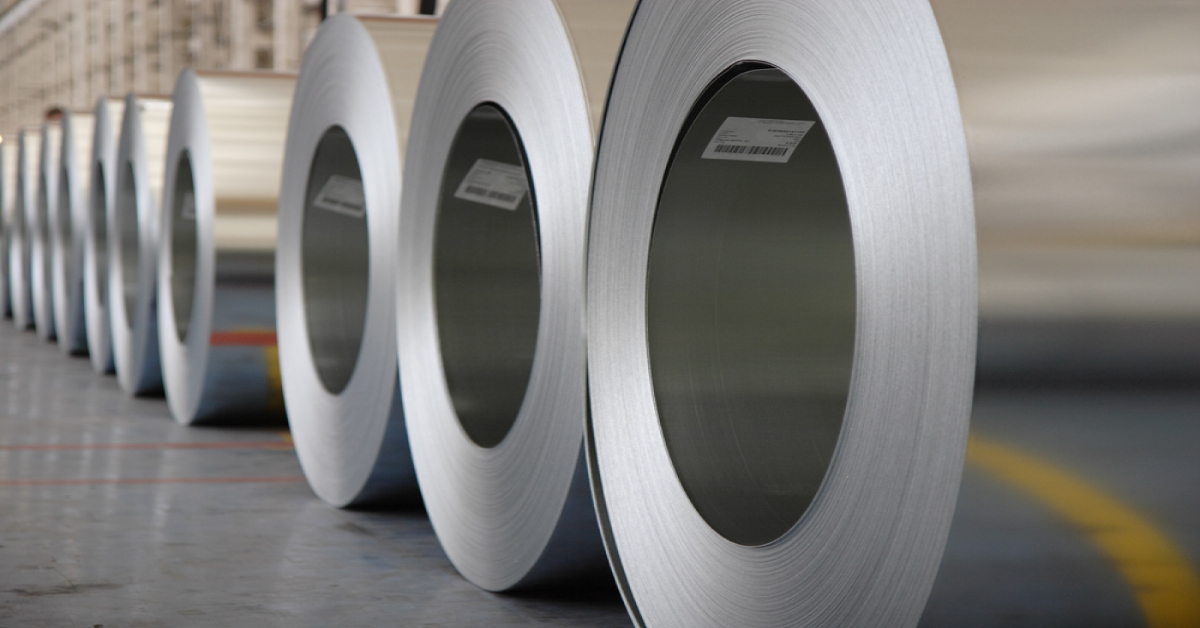
17-7PH, also known as UNS S17700, AMS 5528, DIN/EN 1.4568, JIS SUS 632J1, and AISI 631, is a precipitation-hardening stainless steel known for its high strength and excellent corrosion resistance. It combines the properties of stainless steel with high tensile strength, making it suitable for various high-performance applications.
This alloy is used in aerospace, automotive, and industrial applications where strength, durability, and resistance to stress corrosion are crucial.
17-7PH Sheet | Plate
17-7PH sheets and plates are available in various thicknesses and sizes, suitable for applications requiring high strength and resistance to stress corrosion, including aerospace and automotive components.
17-7PH Round Bar | Rod
Round bars and rods in 17-7PH are available in different diameters and lengths, ideal for precision machining and manufacturing parts that need to withstand high stresses.
17-7PH Strip | Coil
Offered in strips and coils, 17-7PH is used for applications requiring flexible yet strong materials, such as in springs and other high-stress components.
17-7PH Applications
- 17-7PH is used for structural components and aerospace applications where high strength and resistance to corrosion are essential.
17-7PH Properties
- Tensile Strength: Exhibits high tensile strength, typically around 1,200 MPa, making it suitable for demanding applications.
- Density: Approximately 7.8 g/cm³, providing a good strength-to-weight ratio.
- Thermal Conductivity: Moderate thermal conductivity suitable for various applications.
- Corrosion Resistance: Excellent resistance to oxidation and corrosion, especially in environments with high humidity and corrosive chemicals.
Machining 17-7PH
- Cutting: Use high-speed steel or carbide tools for cutting. Precision cutting techniques such as laser or water jet cutting are recommended for detailed work.
- Drilling: Employ carbide drills for drilling 17-7PH. Proper cooling and lubrication are essential to prolong tool life and achieve accurate holes.
- Turning: Carbide inserts are preferred for turning. Maintain consistent cutting speeds and effective cooling to ensure optimal performance.
- Milling: Use carbide end mills with adequate cooling to manage heat and maintain precision during milling operations.
- Grinding: For grinding, use aluminum oxide or CBN wheels to achieve precise tolerances and a high-quality surface finish. Adequate cooling is necessary to prevent overheating and ensure dimensional accuracy.
Chemical Composition
- Aluminum (Al): Min 0.75%, Max 1.50%
- Manganese (Mn): Max 1.00%
- Phosphorus (P): Max 0.05%
- Silicon (Si): Max 1.00%
- Nickel (Ni): Min 6.75%, Max 7.75%
- Sulfur (S): Max 0.03%
- Carbon (C): Max 0.09%
- Chromium (Cr): Min 16.00%, Max 18.00%
Material | Form | Size Inches | SKU Number |
---|---|---|---|
17-7PH | Sheet | Thickness: 0.020" to 0.500"; custom widths and lengths | 17-7PH-SHEET-0.125-12x12 |
17-7PH | Plate | Thickness: 0.500" and up; custom sizes | 17-7PH-PLATE-0.750-24x24 |
17-7PH | Bar/Rod | Diameter: 0.250" to several inches; length up to 36" or more | 17-7PH-BAR-1-36 |
17-7PH | Tube/Pipe | Diameter: 0.5" to several inches; custom wall thickness | 17-7PH-TUBE-1-0.125 |
17-7PH | Wire | Diameter: 0.010" to 0.250"; often supplied in coils | 17-7PH-WIRE-0.050-100 |
17-7PH | Custom Fabrications | Custom dimensions and shapes as required | 17-7PH-CUSTOM-FAB-001 |